Fertigungslinie im U-Shape
Ausgangssituation der Fertigungslinie
Lange Laufwege und Teamarbeitsherausforderungen
Die ursprüngliche Fertigungslinie umfasste neun Stationen, die von einem Team von fünf bis neun Mitarbeitern bedient wurden. Die langen Laufwege zwischen den Stationen erschwerten die Zusammenarbeit und führten zu Effizienzverlusten.
Aushelfen untereinander von vorne nach ganz hinten
Durch die Weitergabe der Teile von einer Station zur nächsten gingen häufig Kleinteile verloren, was die Produktivität beeinträchtigte.
Rückstau von Halbfertigerzeugnissen
Rückstaus von halbfertigen Erzeugnissen zwischen den Stationen erschwerten es den Mitarbeitern, aufgrund der Distanz und des mangelnden Gesamtüberblicks, effektiv zusammenzuarbeiten.
Probleme mit dem Arbeitsplatzdesign
Überdimensionierte Arbeitsflächen
Die Arbeitsplätze verfügten über zu viel Tischfläche, die nicht effizient genutzt wurde. Stattdessen diente sie als Ablagefläche für persönliche Gegenstände, Werkzeuge und Müll.
Lagerung von Montagekomponenten
Hinter den Arbeitsplätzen wurden sämtliche Montagekomponenten gelagert. Die Vielfalt der Materialien in Kombination mit einer hohen Taktzahl führte zu Fehlern bei der Auswahl der benötigten Komponenten.
Von Ihrer Vision
zur realen Lösung
Optimierung der Fertigungslinie nach Lean-Management
U-Form für Flexibilität und Effizienz
Durch die Umgestaltung der Fertigungslinie in eine U-Form verbessern wir die Flexibilität und Effizienz der Zusammenarbeit. Kurze Wege und die Möglichkeit zum schnellen Wechsel der Arbeitsplätze optimieren den Arbeitsfluss.
Neuorganisation der Lagerplätze
Wir trennen die Materiallagerplätze von den Arbeitsstationen. Großbauteile lagern jetzt in einer separaten Kommissionier-Linie, während kleinere Komponenten und Hilfsstoffe ergonomisch und logisch an den Arbeitsplätzen arrangiert sind. Dies fördert die Effizienz und verhindert den Verlust von Kleinteilen.
Automatisierung des Materialtransports
Ein automatisiertes Förderband- und Aufzugsystem übernimmt bei uns die Zu- und Abführung der Baugruppen. Dies verbessert nicht nur die Bereitstellung der benötigten Komponenten in der korrekten Reihenfolge, sondern reduziert auch manuelle Transportaufgaben. Durch die Optimierung des Materialflusses wird die Durchlaufzeit deutlich verringert und das FIFO-Prinzip konsequent eingehalten, was zu effizienteren Produktionsabläufen führt.
Effiziente Raum- und Materialnutzung
Die Einführung von angepassten Montageboards ersetzt herkömmliche Arbeitstische und reduziert überflüssige Stellflächen. Das Kanban-System sorgt für eine optimale Materialversorgung und unterstützt die effiziente Nutzung des Arbeitsraums.
Projektvideo
Ein direkter Blick
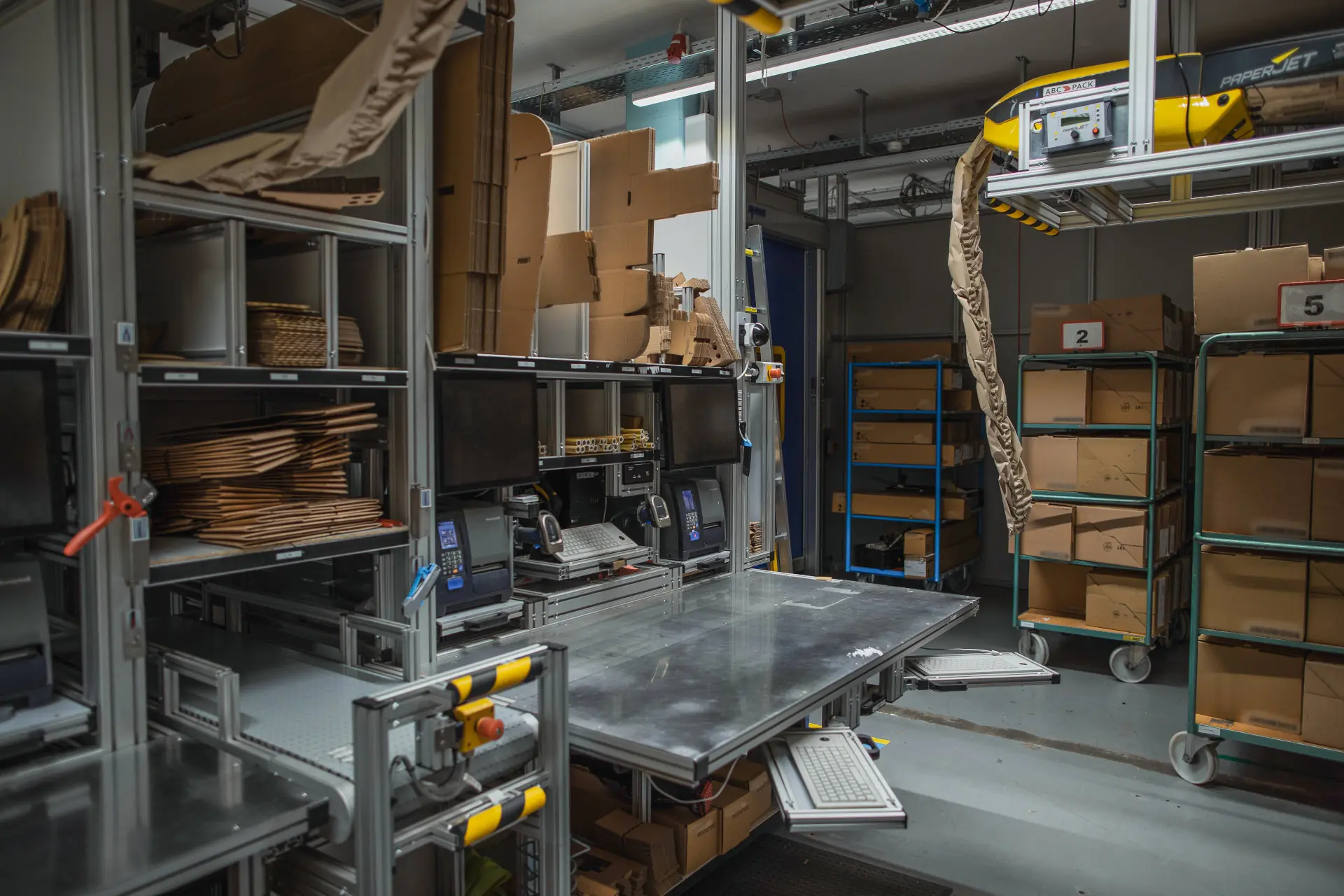
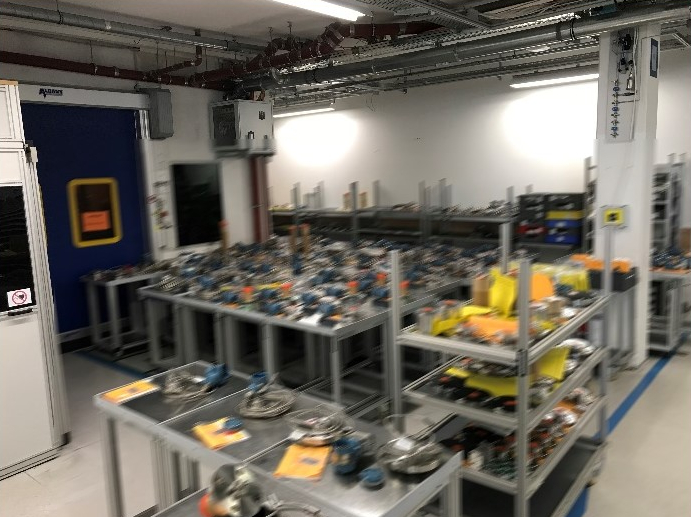