Schweißbereich
Herausforderungen im Schweißbereich
Isolierung und ineffiziente Raumnutzung
Der Schweißbereich ist als geschlossener Raum konzipiert, der vom restlichen Fertigungsbereich isoliert und von außen nicht einsehbar ist. Diese Anordnung führt zu einem Mangel an Überblick und Kontrolle durch die Teamleiter, was die Koordination mit vor- und nachgelagerten Arbeitsgängen erschwert.
Spezialisierung und Flexibilitätsmangel
Jeder Arbeitsplatz im Schweißraum ist auf einen spezifischen Produkttyp spezialisiert, was zwar eine effiziente Fertigung dieses Typs ermöglicht, jedoch das flexible Umstellen auf andere Typen erschwert. Die Umstellung ist mit einem hohen Aufwand verbunden, insbesondere wenn Werkzeuge von weit entfernten Orten geholt werden müssen.
Probleme in der Auftragsreihenfolge
Die Bearbeitung von Fertigungsaufträgen erfolgt nicht zielgerichtet. Aufträge werden ohne feste Reihenfolge kommissioniert, was Mitarbeitern eine freie Wahl bei der Bearbeitung lässt und zu einer erhöhten Anzahl von Halbfertigprodukten führt. Einfachere Aufträge werden bevorzugt, während komplexere vernachlässigt werden, was Durchlaufzeiten verlängert und Lieferverzögerungen verursacht.
Folgeprobleme durch zu große Flexibilität
Die im Voraus erfolgte Bevorratung blockiert eine große Fläche für Halbfertigprodukte. Bei Verzögerungen oder Maschinenausfällen in nachgelagerten Arbeitsgängen ist kein Abfluss möglich, was die Produktion zusätzlich behindert. Die vermeintliche Flexibilität führt zu Verstopfungen in der Produktion, unnötigen innerbetrieblichen Transporten und Verzögerungen im Dominoeffekt.
Von Ihrer Vision
zur realen Lösung
Durchführung der Wertstromanalyse
Wertstromanalyse zur Problemidentifikation
Zur Identifikation der Problematik und möglicher Folgeeffekte wurde eine umfassende Wertstromanalyse ("Value Stream Map") durchgeführt. Dieser Prozess erforderte die Zusammenarbeit aller beteiligten Mitarbeiter, einschließlich der vor- und nachgelagerten Arbeitsprozesse und der Informationsflüsse, um einen optimierten Soll-Ablauf zu entwerfen.
Anpassung an lokale Gegebenheiten
Der ideale Soll-Ablauf wurde unter Berücksichtigung der unveränderlichen strukturellen Gegebenheiten und der räumlichen Kapazitäten angepasst. Wichtig war dabei, sich nicht durch vorgefasste Annahmen einschränken zu lassen und auch tiefgreifende Veränderungen in Betracht zu ziehen.
Entwicklung von Layoutideen
Vergleich von Layoutszenarien
Es wurden zwei Layoutszenarien entwickelt, die einen umfassenden strukturellen Umbau mit einer kleineren Umstrukturierung verglichen. Diese Szenarien wurden hinsichtlich Vor- und Nachteilen sowie Kapital- und Zeiteinsatz bewertet.
Entscheidung für umfassenden Umbau
Nach Abwägung aller Faktoren entschieden sich die Verantwortlichen für einen umfassenden Umbau, der nicht nur bestehende Probleme löst, sondern auch Kapazität, Flexibilität und Übersichtlichkeit verbessert.
Umsetzung des Umbauplans
Kernpunkte des Umbaus
Der Umbau umfasste das Ersetzen des Schweißraums durch individuelle Schweißkabinen, die Anpassung der Infrastruktur, das Entwerfen neuer Prozessabläufe, die Schulung der Mitarbeiter und die Implementierung des DMAIC-Konzepts zur kontinuierlichen Verbesserung.
Einführung von FIFO-Lanes
Eine wesentliche Prozessveränderung war die Implementierung von FIFO-Lanes, um einen geordneten und optimierten Materialfluss zu gewährleisten.
Ergebnisse des Umbaus
Verbesserung der Produktionsprozesse
Durch den Umbau wurden alle identifizierten Probleme nachhaltig gelöst, die Durchlaufzeiten um durchschnittlich 8% verkürzt und die Arbeitsbedingungen für die Mitarbeiter verbessert.
Modernisierung der Infrastruktur
Teile der elektrischen Infrastruktur wurden erneuert, insbesondere die Beleuchtung, die auf energieeffiziente LED-Technik umgestellt wurde.
Effiziente Durchführung
Der gesamte Umbau wurde innerhalb von nur sechs Tagen von einem interdisziplinären Team aus insgesamt 60 Personen durchgeführt. EPIC & I fungierte dabei als zentrale Schnittstelle. Die beteiligten Gewerke umfassten Trockenbau, Hochdruckleitungen für Edelgase, Lüftungs- und Klimatechnik, Elektrik sowie Maschinenbau, was die Komplexität und den Erfolg des Projekts unterstreicht.
Projektvideo
Ein direkter Blick
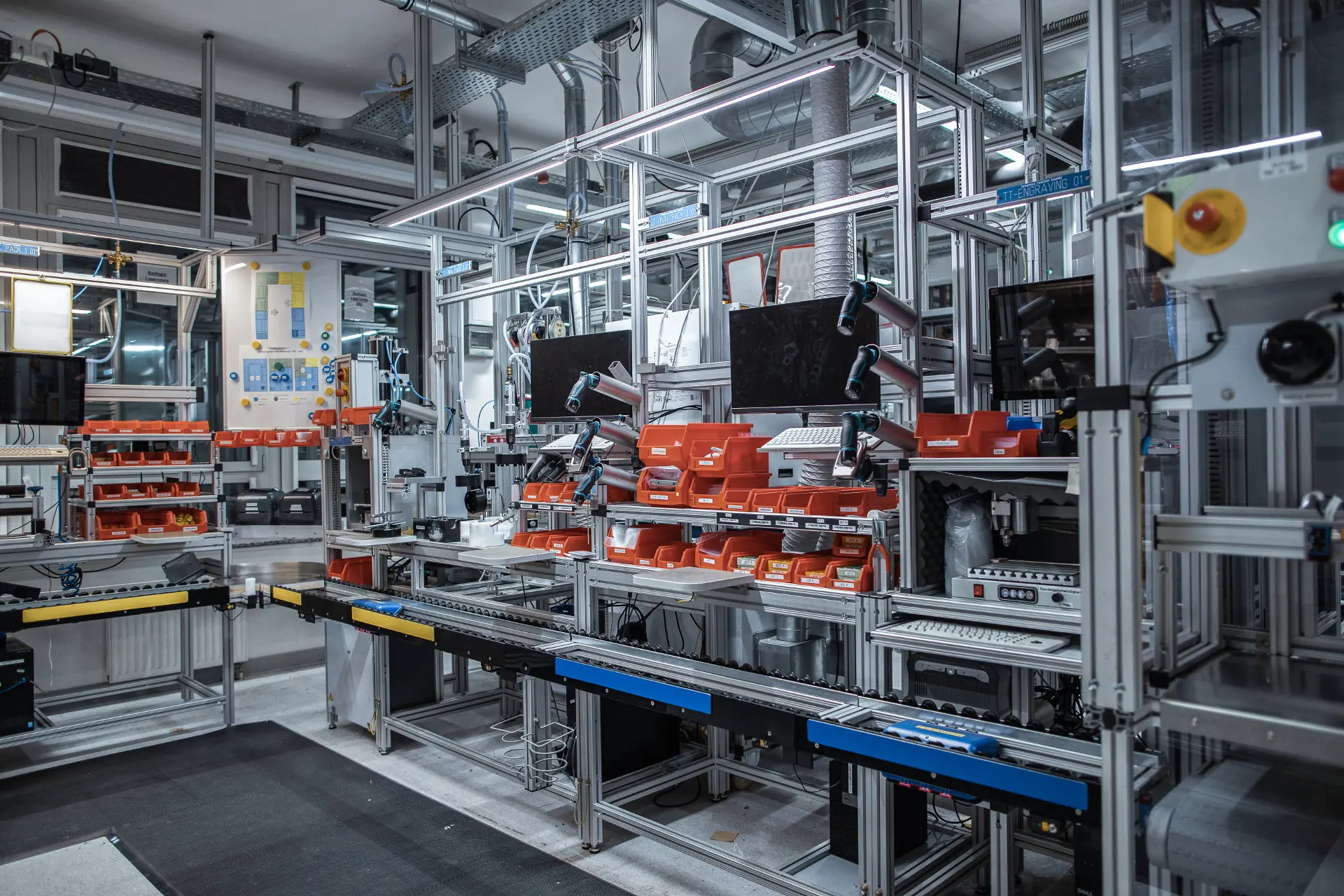
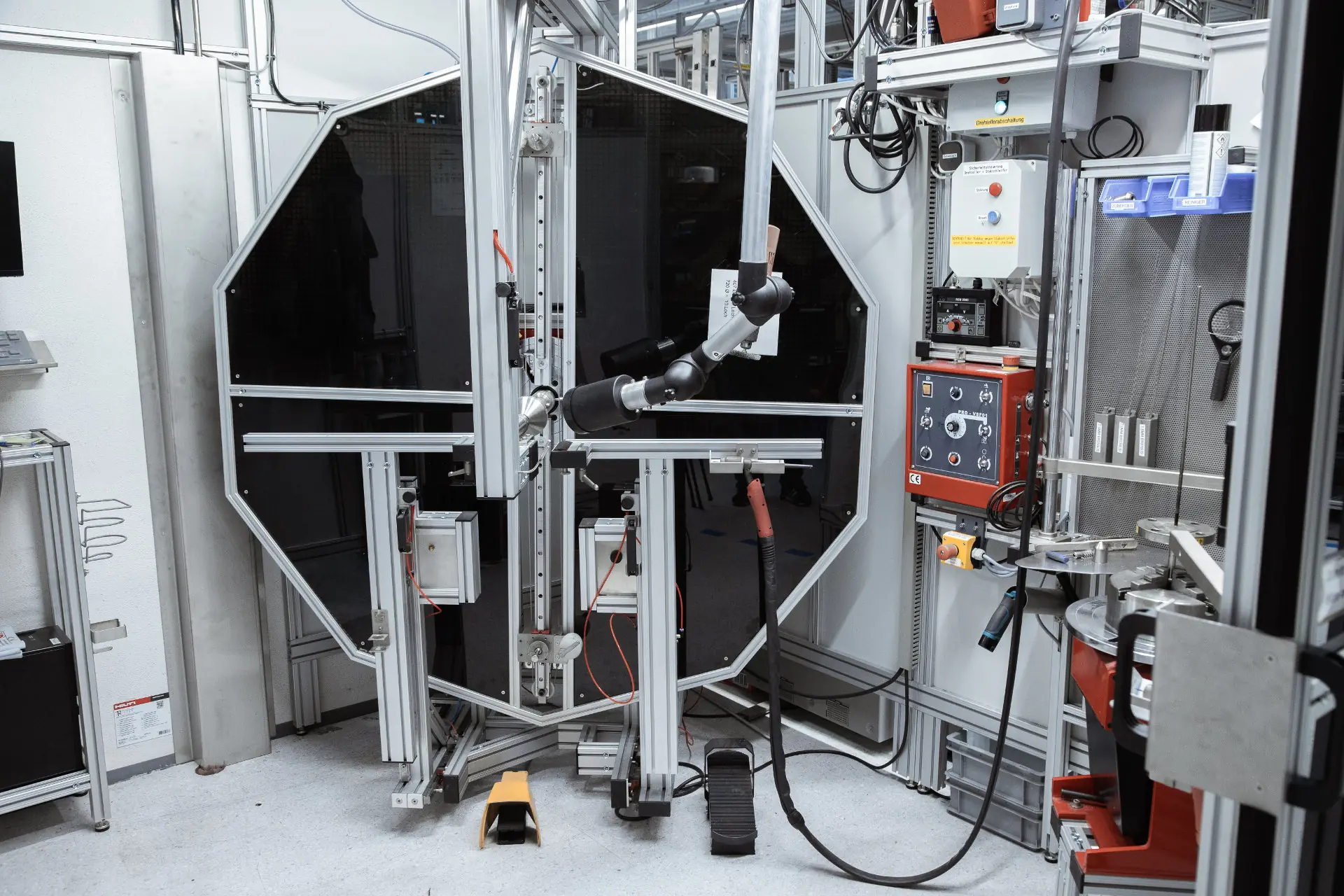