Sondermaschinenbau & Automatisierung
Hochdruckprüfstation
Grundlegende Prüfverfahren in der Fertigung
1. Lecktest
- Verfahren: Der Prüfling wird mit einem Druck von 24 bis 1655 Bar beaufschlagt.
- Messung: Nach 10 Minuten wird der Druckabfall gemessen, um die Dichtheit zu überprüfen.
2. Stresstest
- Verfahren: Der Prüfling wird einer ständigen Druckbeaufschlagung und Entlüftung mit knapp 500 Bar unterzogen.
- Ziel: Überprüfung der Verschiebung des Nullpunktes durch den Druck.
Identifizierte Grundprobleme
Kapazitätslimitationen
- Die Kapazität jedes Arbeitsschritts ist begrenzt, was bei Lastspitzen zu Rückstau führen kann, während andere Stationen möglicherweise unterausgelastet sind.
Begrenzte Flexibilität der Stationen
- Bestehende Prüfstationen können vier Prüflinge gleichzeitig nur mit denselben Druckstufen testen, was die Auslastung erschwert und einen Engpass schafft.
Fehlende Spezifikationen und manuelle Prozesse
- Maschinen sind auf maximal 1024 Bar limitiert, was nicht alle Kundenspezifikationen abdeckt.
- Die Durchführung und Ergebniserfassung der Tests ist vollständig manuell und abhängig von der Genauigkeit der Mitarbeiter.
Probleme mit dem Prüfmedium
- Als Prüfmedium dient ein Wasser-Alkohol-Gemisch, das eine nachfolgende Trocknung der Prüflinge erfordert.
Von Herausforderungen zu Ergebnissen
Von Ihrer Vision
zur realen Lösung
Konzeption der neuen Prüfanlage
Unabhängige Druckkammern
- Die Anlage besteht aus zwei Druckkammern, die unabhängig voneinander beladen, gestartet und entladen werden können, selbst wenn sich die andere Kammer in einem Prüfzyklus befindet.
Individualisierte Druckprüfungen
- Innerhalb jeder Kammer kann jeder der vier Anschlüsse individuell mit unterschiedlichen Drücken beaufschlagt werden, was nicht nur die Durchlaufzeit, den Zwischenlagerplatz und die Produktionsreihenfolge optimiert, sondern auch das vorherige Sortieren und Lagern der Prüflinge bis zu einer vollen Auslastung der Prüfkammer überflüssig macht. Zudem ist jeder Anschluss einzeln überwacht, was eine sofortige Identifikation undichter Geräte ermöglicht und erkennen lässt, welche direkt weiterverarbeitet werden können.
Fortführung bei Ausfall
- Bei Ausfall eines Anschlusses können die übrigen Anschlüsse ohne Beeinträchtigung weiter betrieben werden, was die Zuverlässigkeit der Anlage erhöht.
Flexibilität in den Prüfverfahren
- Jede Kammer lässt sich per Knopfdruck für beide Prüfverfahren umstellen, was eine flexible Reaktion auf Lastspitzen ermöglicht.
Automatisierung und Effizienz
Datenbankgesteuerte Testparameter
- Die Testparameter werden datenbankgesteuert und automatisch durch Scannen der Laufkarte des Prüflings abgerufen, was manuelle Fehlerquellen reduziert.
Automatische Protokollierung
- Testergebnisse werden automatisch in der Produktionssteuerungssoftware protokolliert, was eine lückenlose Dokumentation und Nachvollziehbarkeit sicherstellt.
Identifikation von Leckagen
- Bei einer Leckage wird sofort angezeigt, welcher Anschluss betroffen ist, was eine schnelle Nacharbeitung ermöglicht.
Innovatives Prüfmedium
Einsatz eines neuartigen Mediums
- Das verwendete Medium von 3M verdunstet rückstandsfrei und benötigt keine besondere Absauganlage, was die Handhabung vereinfacht.
Direkte Weiterverarbeitung
- Prüflinge können ohne Trocknungszeit direkt weiterverarbeitet werden, was den Gesamtprozess beschleunigt.
Erweiterung der Prüfkapazität
Hochdruckprüfungen
- Die Erhöhung der Prüfkapazität auf 1655 Bar, mit der Option auf Erweiterung bis zu 2200 Bar, ermöglicht eine breitere Abdeckung von Kundenspezifikationen.
Flexibler Anschluss der Prüflinge
- Speziell angefertigte Hochdruckprüfadapter, die von Hand und ohne Werkzeug eingedreht werden können, erhöhen nicht nur die Flexibilität, sondern auch die Sicherheit bei der Anwendung. Diese benutzerfreundliche Handhabung bietet einen großen Vorteil, ohne dabei die Sicherheit zu beeinträchtigen.
Qualitätssicherung
Regelmäßige Selbsttests
- Durch tägliche Selbsttests der Prüfstation auf Leckagen, die von der Software automatisch durchgeführt und in die Prüfergebnisse eingerechnet werden, wird eine hohe Zuverlässigkeit und Genauigkeit der Testergebnisse sichergestellt. Dies gewährleistet, dass eventuelle Überschreitungen der Toleranzgrenzen nicht unentdeckt bleiben.
Video
Projektvideo
Ein direkter Blick
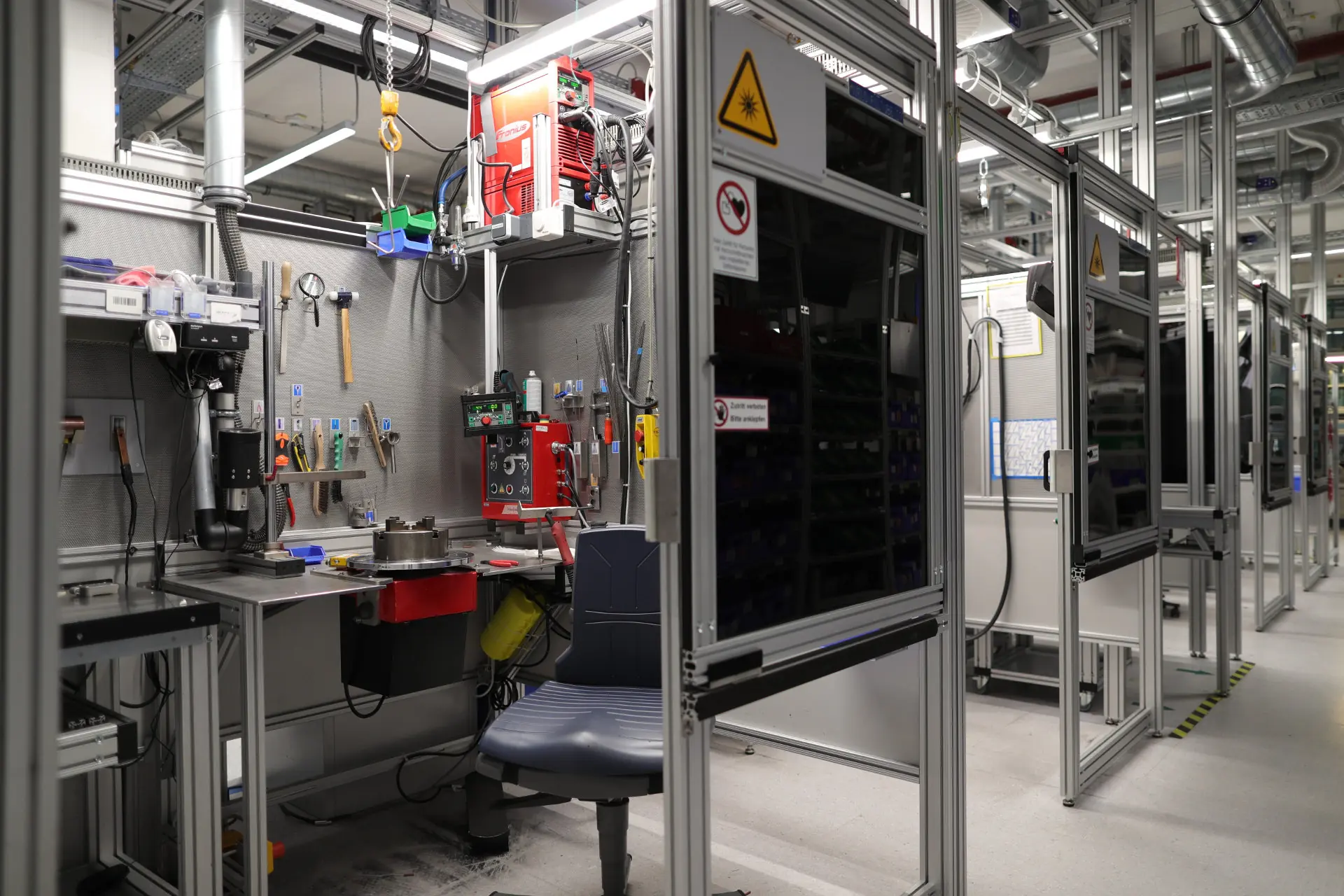
Arbeitsstationen & Fertigungsequipment
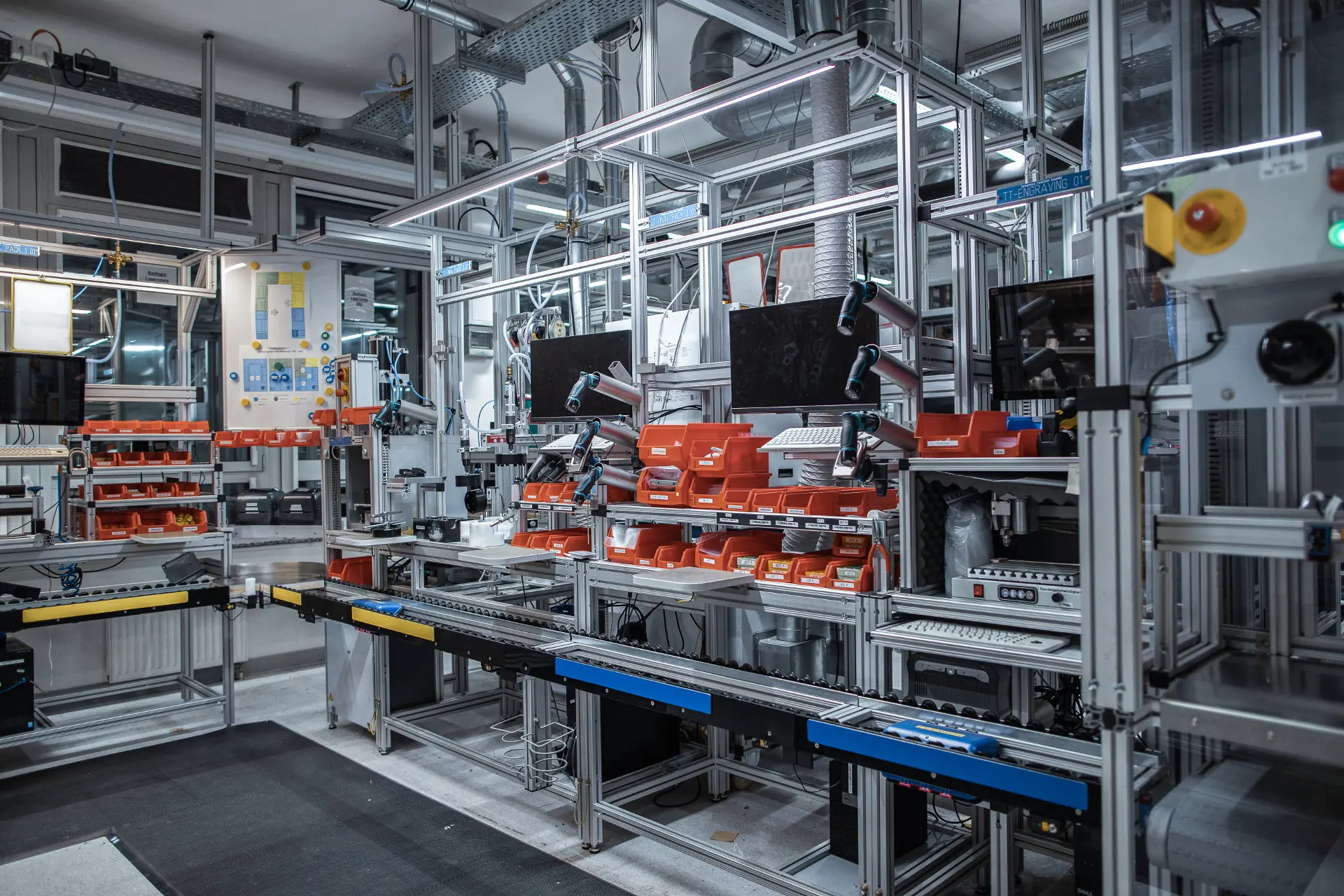
Arbeitsstationen & Fertigungsequipment
Prozessoptimierung