Special machine construction & automation
High Pressure Test Station
Basic testing methods in manufacturing
1. Leak test
- proceedings: The test sample is exposed to a pressure of 24 to 1655 bar.
- measurement: After 10 minutes, the pressure drop is measured to check the tightness.
2nd stress test
- proceedings: The test sample is subjected to continuous pressurization and venting at just under 500 bar.
- target: Verification of the shift of the zero point due to pressure.
Key issues identified
capacity limitations
- The capacity of each work step is limited, which can lead to backlogs during peak loads, while other stations may be underutilized.
Limited flexibility of stations
- Existing test stations can test four candidates at the same time only with the same pressure levels, which makes workload difficult and creates a bottleneck.
Lack of specifications and manual processes
- Machines are limited to a maximum of 1024 bar, which does not cover all customer specifications.
- The execution and recording of the results of the tests is completely manual and depends on the accuracy of the employees.
Test medium problems
- A water-alcohol mixture, which requires subsequent drying of the test specimens, is used as the test medium.
From challenges to results
From your vision
to the real solution
Design of the new testing system
Independent pressure chambers
- The system consists of two pressure chambers which can be loaded, started and unloaded independently of each other, even when the other chamber is in a test cycle.
Individualized pressure tests
- Within each chamber, each of the four connections can be individually pressed with different pressures, which not only optimizes the processing time, the interim storage location and the production sequence, but also makes the previous sorting and storage of the test specimens until the test chamber is fully utilized. In addition, each connection is individually monitored, which enables immediate identification of leaky devices and allows you to identify which can be further processed directly.
Continuation in case of failure
- If one connection fails, the remaining connections can continue to operate without impairment, which increases the reliability of the system.
Flexibility in testing procedures
- Each chamber can be converted for both test methods at the push of a button, which enables a flexible response to load peaks.
Automation and efficiency
Database-driven test parameters
- The test parameters are database-controlled and automatically retrieved by scanning the test item's running card, which reduces manual sources of error.
Automatic logging
- Test results are automatically logged in production control software, which ensures complete documentation and traceability.
Identification of leaks
- In the event of a leak, it is immediately shown which connection is affected, which enables rapid rework.
Innovative test medium
Use of a novel medium
- The 3M medium used evaporates without leaving any residue and does not require a special extraction system, which makes handling easier.
Direct further processing
- Test samples can be further processed directly without drying time, which speeds up the overall process.
Expanding testing capacity
high pressure tests
- The increase in testing capacity to 1655 bar, with the option to expand up to 2200 bar, enables a wider coverage of customer specifications.
Flexible connection of test specimens
- Specially manufactured high-pressure test adapters, which can be screwed in by hand and without tools, not only increase flexibility but also safety during use. This user-friendly operation offers a major advantage without sacrificing safety.
Quality Assurance
Regular self-tests
- Daily self-tests by the test station for leaks, which are carried out automatically by the software and included in the test results, ensure a high level of reliability and accuracy of the test results. This ensures that any violations of the tolerance limits do not go undetected.
Video
Project video
A direct look
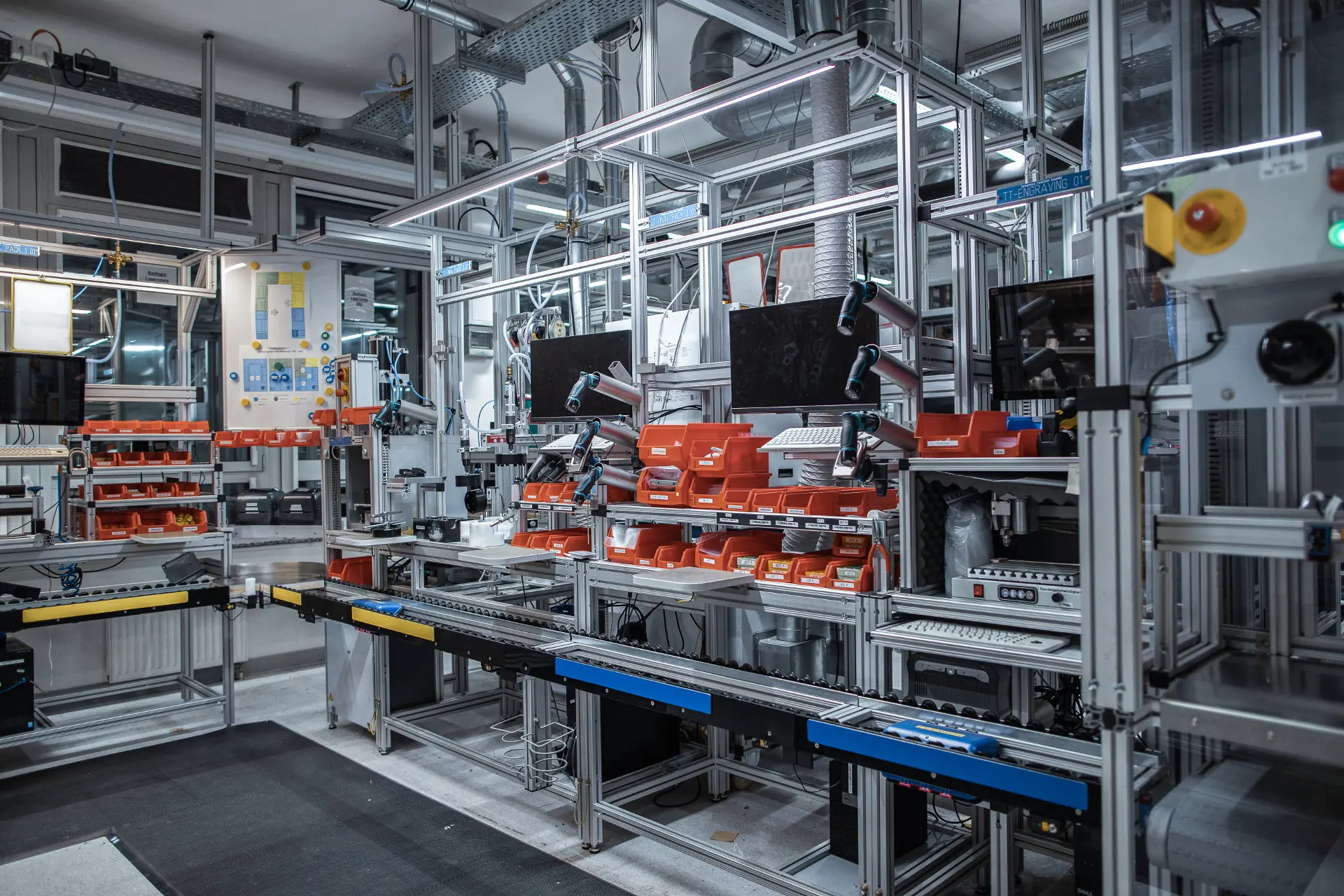
Workstations & manufacturing equipment
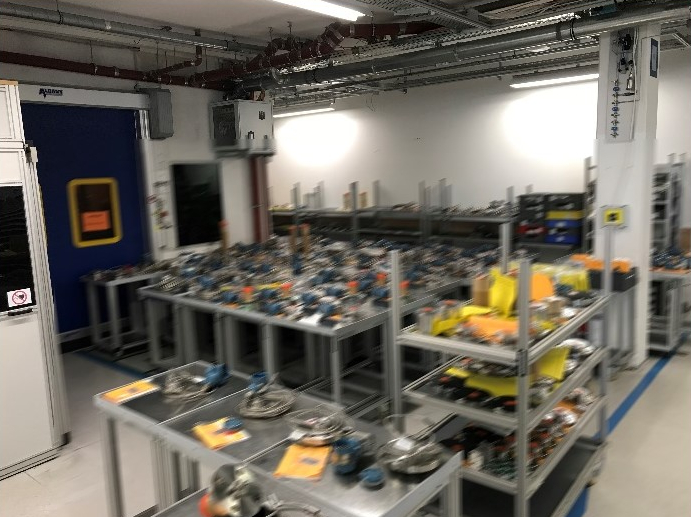
Layout concepts & modifications