Schweißkabine
Neukonzeption der Schweißkabinen im Fertigungsbereich
Ganzheitliches Konzept
Im Rahmen eines umfangreichen Umbauprojekts wurden die Schweißkabinen komplett neu gestaltet. Das zugrundeliegende Konzept berücksichtigt eine Vielzahl von Anforderungen der verschiedenen Arbeitsplätze, um eine effiziente und ergonomische Arbeitsumgebung zu schaffen.
Standardisierte Gestaltung
Jede Kabine folgt dem gleichen Designprinzip, das darauf abzielt, sämtliche Schweißungen ohne Notwendigkeit des Umklemmens der Masse zu ermöglichen. Dies spiegelt die Vielfalt der Schweißanforderungen wider, von einfachen Vormontageschweißungen bis hin zu komplexeren Aufgaben wie tieferem Einbrand und mehrschichtigen Schweißungen.
Anpassung an diverse Bauteilgrößen
Die Bauteilgrößen variieren erheblich, von wenigen 100g bis zu 200kg, und umfassen Dimensionen von 3mm (Kapillarrohre) bis zu einem Flanschdurchmesser von 400mm und einer Stärke von 70mm. Dies erfordert eine flexible Anpassung der Schweißvorrichtungen an die Größe der Bauteile.
Spezialvorrichtungen für qualitativ hochwertige Schweißnähte
Für größere Bauteile, die hohe Qualitätsansprüche erfüllen müssen, ist der Einsatz von Drehtellern unerlässlich, um ein kontinuierliches Schweißen ohne Unterbrechungen zu gewährleisten. Besonders kritisch ist dabei, dass sich dünnwandige Kapillarrohre während des Drehvorgangs nicht verwinden und somit keine unbeabsichtigten Sollbruchstellen entstehen.
Ergonomische Verbesserungen und Sichtschutz
Die Neugestaltung umfasste auch die Einführung von ergonomischeren Arbeitsstationen und die Verbesserung der Sichtbarkeit des Schweißbereichs für Teamleiter, während gleichzeitig außenstehende Personen vor den Gefahren des Verblitzens geschützt werden. Werkzeuge und Verbrauchsmaterialien sowie IT-Equipment wurden so integriert, dass sie den Arbeitsplatz nicht unnötig einengen und die Arbeitsfläche optimal genutzt werden kann.
Von Ihrer Vision
zur realen Lösung
Innovative Gestaltung universeller Schweißarbeitsplätze
Einzigartige Lösung für vielseitige Anforderungen
Die Neugestaltung der Schweißkabinen folgt einem umfassenden Ansatz, der darauf abzielt, den Mitarbeitern die Durchführung sämtlicher Arbeitsvorgänge an einem einzigen, ergonomisch optimierten Arbeitsplatz zu ermöglichen. Dieser Ansatz entspricht der Idee einer "eierlegenden Wollmilchsau" und stellt sicher, dass kein Arbeitsplatzwechsel für unterschiedliche Schweißaufgaben erforderlich ist.
Grundkonzept der Arbeitsstationen
Mit einem standardisierten Grundaufbau von 2,00 x 2,50 Metern sind alle Stationen aus Aluminiumprofilen und Schweißschutzscheiben konstruiert. Diese Konstruktion ermöglicht eine Rundumsicht von außen, während gleichzeitig der notwendige Schutz für außenstehende Personen gewährleistet wird. Zudem ist jede Kabine mit einer individuell regelbaren Klima- und Absauganlage ausgestattet, was den Komfort für die Mitarbeiter erhöht.
Ausstattung und Funktionalität
Jede Kabine verfügt über ein spezielles Set an Schweißvorrichtungen, integrierte Halterungen für IT-Equipment, Werkzeuge und Hilfsmaterialien. Alle notwendigen Materialien sind so arrangiert, dass sie leicht zugänglich sind und die Arbeitsfläche für die eigentlichen Schweißarbeiten freibleibt. Touchscreens, die auch mit Schweißhandschuhen bedienbar sind, erleichtern zudem die Arbeit.
Besonderheiten der Arbeitsflächen
Die Arbeitsflächen bestehen aus massiven Edelstahlplatten, die stark genug sind, um auch schwerste Bauteile zu tragen. Diese Platten sind direkt mit dem Massepotenzial des Schweißgeräts verbunden und fungieren somit als universelle Schweißarbeitsfläche. Ein integrierter Drehteller in der Arbeitsplatte erleichtert das Bearbeiten der Bauteile.
Anpassungen für spezielle Schweißaufgaben
Um die Herausforderungen bei der Bearbeitung von Bauteilen auf Edelstahl-Transportwagen zu überwinden, haben wir ein innovatives Konzept entwickelt: Ein etwa 1 kg schwerer Kupferblock, der auf die Tischplatte gelegt wird und direkt an die Masse angeschlossen ist, verwandelt den Wagen durch einfaches Auflegen in einen vollwertigen Schweißarbeitsplatz. Dieses System eliminiert die Notwendigkeit, eine Schweißklemme mit Kraftaufwand zu befestigen und reduziert gleichzeitig das Zittern der Mitarbeiter, indem es eine stabile und sichere Schweißfläche schafft, ohne das Risiko von Beschädigungen. Zudem ermöglicht das Schweißen direkt auf dem Wagen, dass das Anheben schwerer Werkstücke entfällt, was das Risiko von Beschädigungen erheblich reduziert.
Projektvideo
Ein direkter Blick

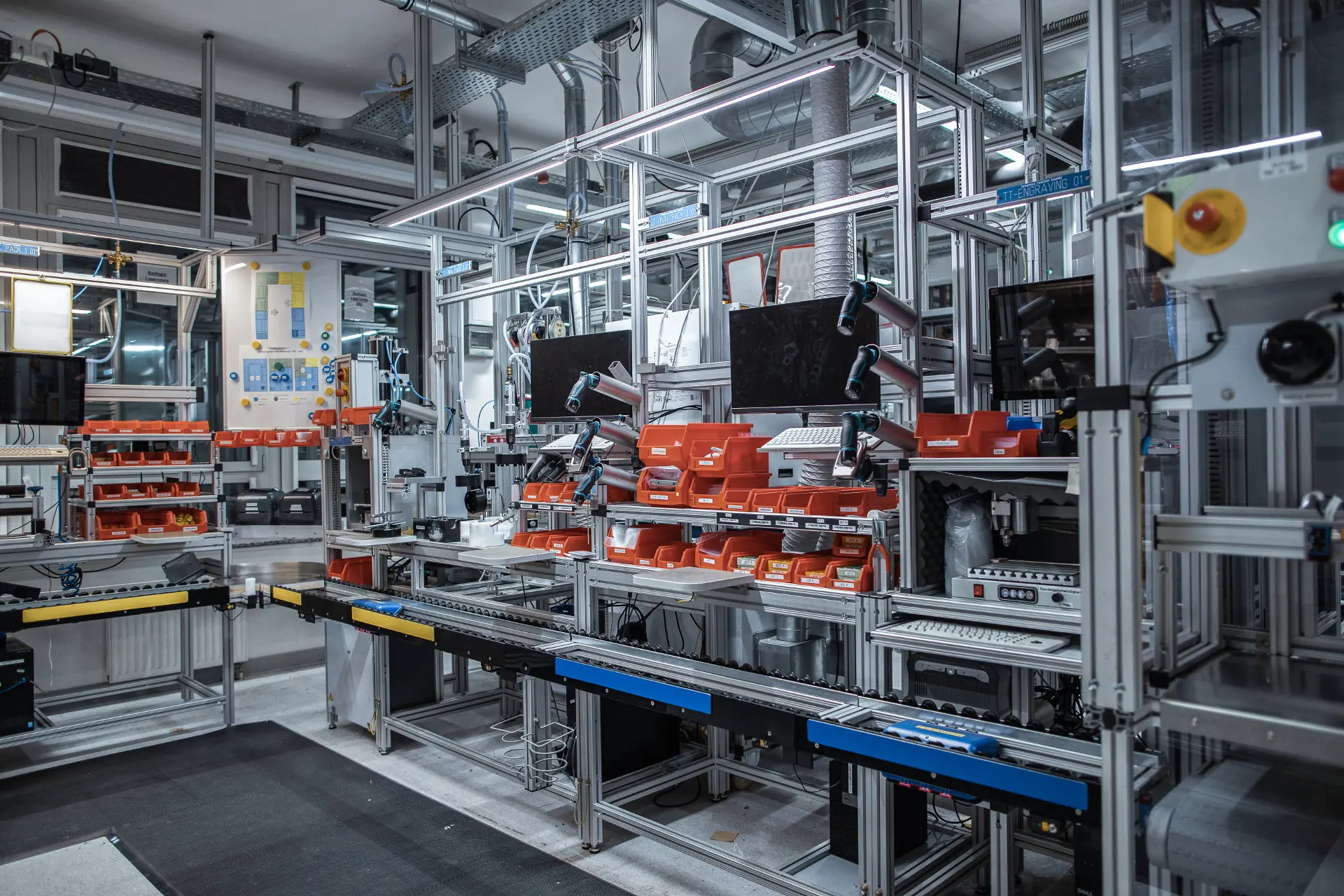