Welding Booth
New design of welding booths in the production area
Holistic concept
As part of an extensive renovation project, the welding cabins were completely redesigned. The underlying concept takes into account a wide range of requirements of the various workplaces in order to create an efficient and ergonomic working environment.
Standardised design
Each cabin follows the same design principle, which aims to make all welding possible without the need to clamp the mass. This reflects the variety of welding requirements, from simple pre-assembly welding to more complex tasks such as deeper penetration and multi-layer welds.
Adaptation to various component sizes
The component sizes vary considerably, from a few 100 g to 200 kg, and include dimensions of 3 mm (capillary tubes) up to a flange diameter of 400 mm and a thickness of 70 mm. This requires a flexible adjustment of the welding devices to the size of the components.
Special devices for high-quality welds
For larger components that must meet high quality requirements, the use of turntables is essential to ensure continuous welding without interruptions. It is particularly critical that thin-walled capillary tubes do not twist during the turning process and therefore no unintentional predetermined breaking points occur.
Ergonomic improvements and privacy
The redesign also included the introduction of more ergonomic workstations and improving the visibility of the welding area for team leaders, while protecting outsiders from the dangers of lightning. Tools and consumables as well as IT equipment have been integrated in such a way that they do not unnecessarily restrict the workplace and that the work area can be used optimally.
From your vision
to the real solution
Innovative design of universal welding workstations
Unique solution for a wide range of requirements
The redesign of the welding booths follows a comprehensive approach that aims to enable employees to carry out all work processes at a single, ergonomically optimized workplace. This approach is in line with the idea of an “egg-laying woolly milk sow” and ensures that there is no need to change jobs for different welding tasks.
Basic concept of workstations
With a standardized basic structure of 2.00 x 2.50 meters, all stations are constructed from aluminum profiles and welding shields. This construction allows all-round visibility from outside, while at the same time ensuring the necessary protection for outsiders. In addition, each cabin is equipped with an individually controlled air conditioning and extraction system, which increases comfort for employees.
Features and functionality
Each cabin has a special set of welding devices, integrated holders for IT equipment, tools and auxiliary materials. All necessary materials are arranged in such a way that they are easily accessible and the work surface remains free for the actual welding work. Touch screens, which can also be operated with welding gloves, also make work easier.
Special features of the work surfaces
The work surfaces consist of solid stainless steel plates, which are strong enough to support even the heaviest components. These plates are directly connected to the mass potential of the welding machine and therefore function as a universal welding work surface. An integrated turntable in the worktop makes it easy to process the components.
Adjustments for special welding tasks
In order to overcome the challenges of processing components on stainless steel transport trolleys, we have developed an innovative concept: A copper block weighing around 1 kg, which is placed on the table top and is connected directly to the ground, transforms the trolley into a full-fledged welding workstation simply by placing it on. This system eliminates the need to apply force to secure a welding clamp while reducing employee shaking by creating a stable and safe welding surface without the risk of damage. In addition, welding directly on the trolley makes it possible to eliminate the need to lift heavy workpieces, which significantly reduces the risk of damage.
Project video
A direct look
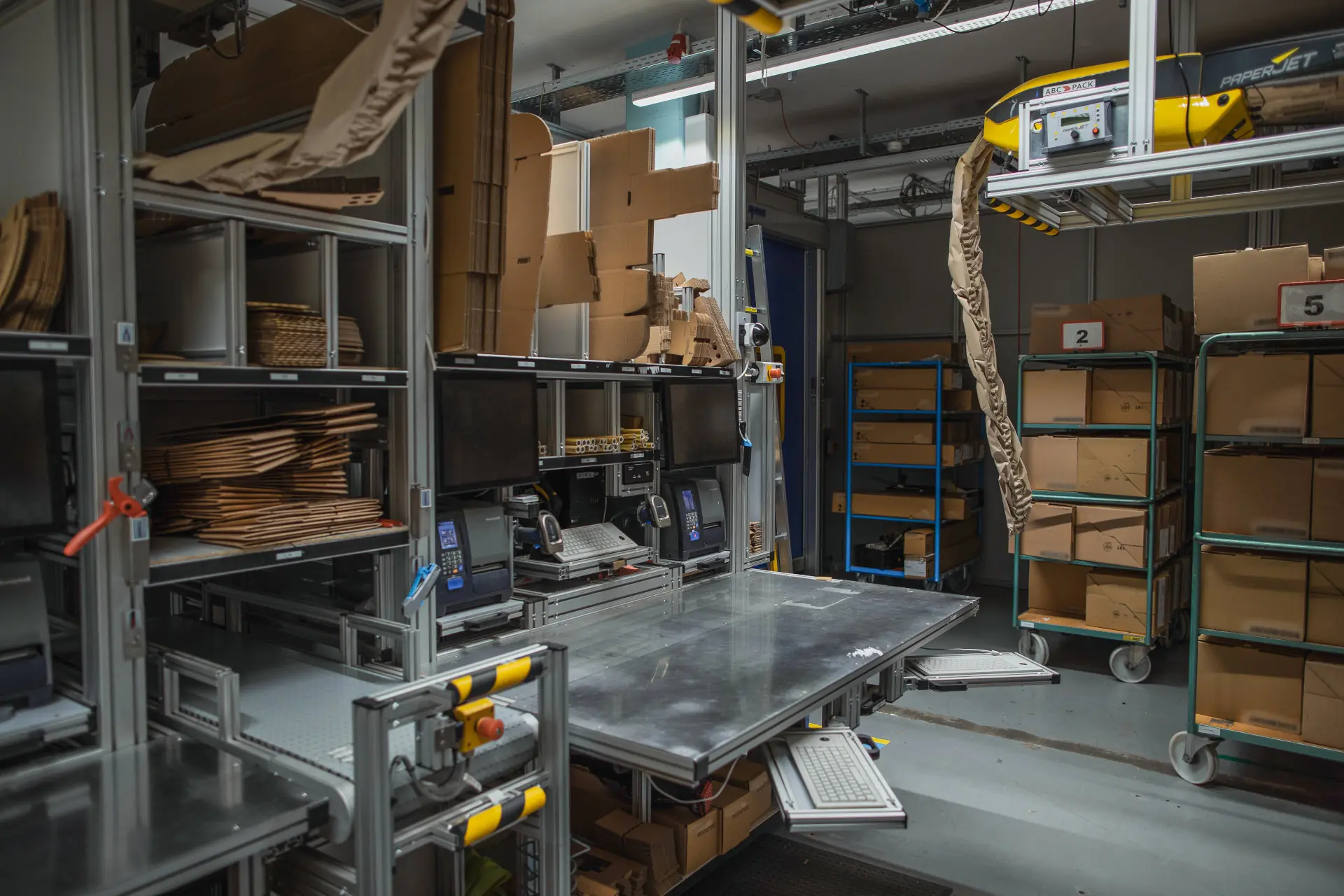
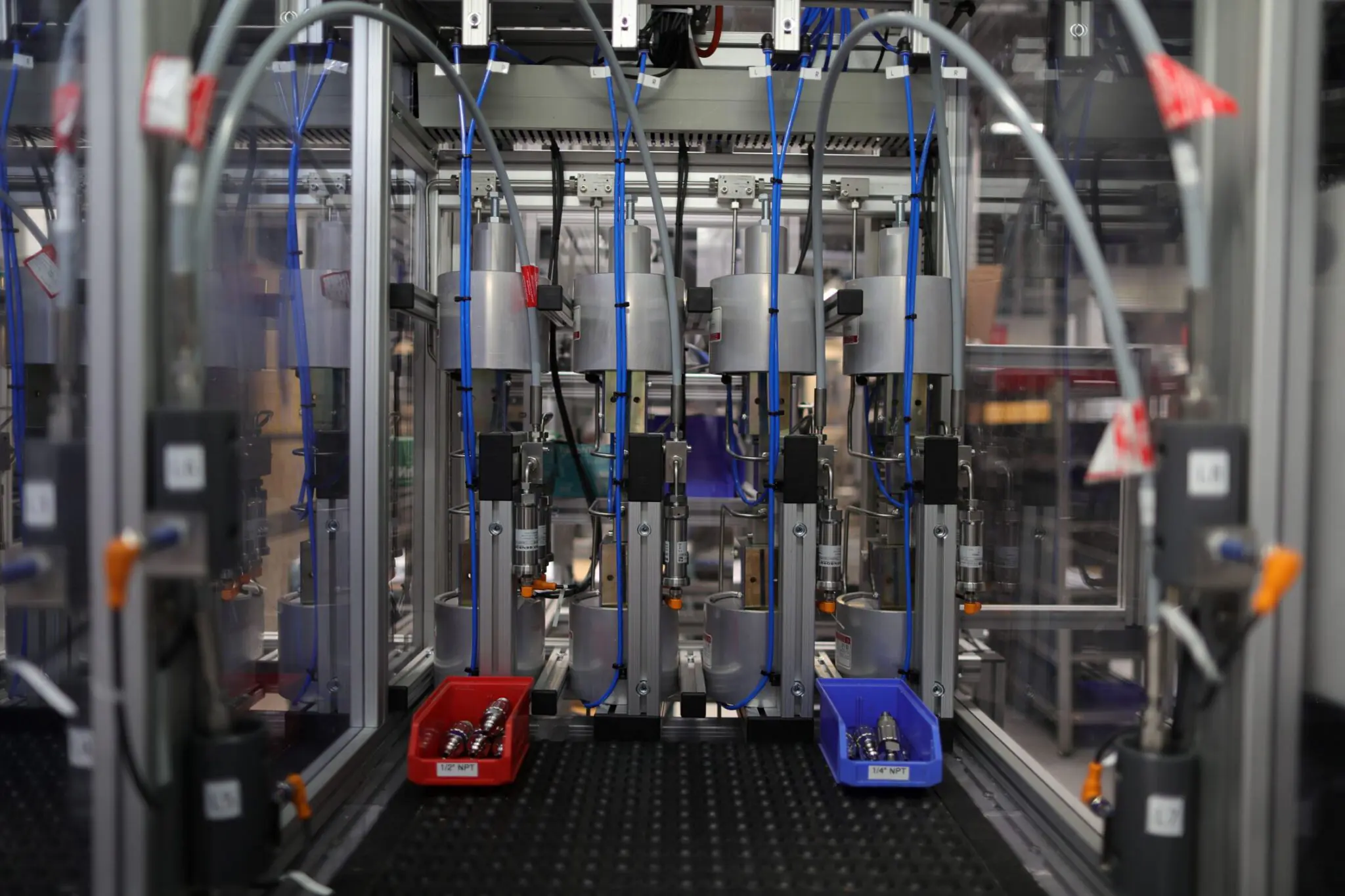