Welding Area
Welding challenges
Isolation and inefficient use of space
The welding area is designed as a closed space that is isolated from the rest of the production area and cannot be seen from outside. This arrangement results in a lack of overview and control by team leaders, which makes coordination with upstream and downstream work processes difficult.
Specialization and lack of flexibility
Each workstation in the welding room specializes in a specific type of product, which enables efficient production of this type, but makes it difficult to flexibly switch to other types. The changeover involves a great deal of effort, especially when tools have to be fetched from distant locations.
Order order issues
Construction orders are not processed in a targeted manner. Orders are picked in no fixed order, which gives employees a free choice when processing and results in an increased number of semi-finished products. Simpler orders are preferred, while more complex ones are neglected, which increases turnaround times and causes delivery delays.
Consequential problems due to too much flexibility
The storage carried out in advance blocks a large area for semi-finished products. In the event of delays or machine failures in downstream operations, no outflow is possible, which further hinders production. The alleged flexibility leads to blockages in production, unnecessary intra-company transport and delays with a domino effect.
From your vision
to the real solution
Carrying out the value stream analysis
Value stream analysis for problem identification
A comprehensive value stream analysis (“Value Stream Map”) was carried out to identify the problem and possible consequences. This process required the collaboration of all employees involved, including upstream and downstream work processes and information flows, in order to design an optimized target process.
Adapting to local conditions
The ideal target process was adjusted taking into account the unchanging structural conditions and spatial capacities. It was important not to be limited by preconceived assumptions and also to consider far-reaching changes.
Development of layout ideas
Comparing layout scenarios
Two layout scenarios were developed which compared a comprehensive structural reorganization with a smaller restructuring. These scenarios were assessed in terms of advantages and disadvantages as well as the use of capital and time.
Decision for comprehensive renovation
After weighing up all factors, those responsible decided on a comprehensive restructuring that not only solves existing problems, but also improves capacity, flexibility and clarity.
Implementation of the renovation plan
Key points of the renovation
The renovation included replacing the welding room with individual welding booths, adapting the infrastructure, designing new process flows, training employees and implementing the DMAIC concept for continuous improvement.
Introduction of FIFO lanes
A significant process change was the implementation of FIFO lanes to ensure an orderly and optimized material flow.
Results of the renovation
Improving production processes
As a result of the renovation, all identified problems were solved sustainably, processing times were reduced by an average of 8% and improved working conditions for employees.
Modernizing infrastructure
Parts of the electrical infrastructure were renewed, in particular the lighting, which was converted to energy-efficient LED technology.
Efficient execution
The entire renovation was carried out within just six days by an interdisciplinary team of a total of 60 people. EPIC & I acted as a central interface. The trades involved included drywall, high-pressure pipes for noble gases, ventilation and air-conditioning technology, electrical and mechanical engineering, which underlines the complexity and success of the project.
Project video
A direct look
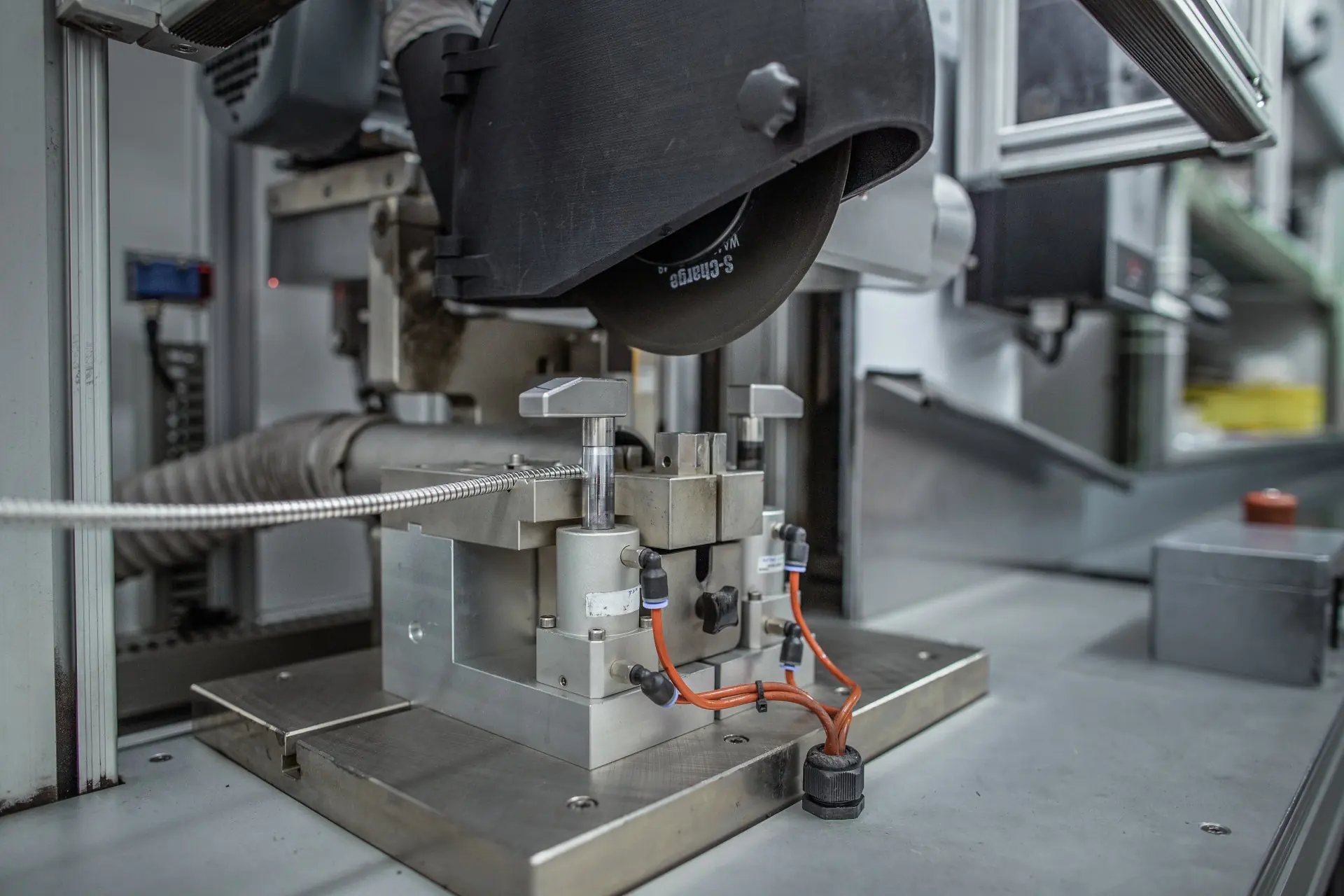
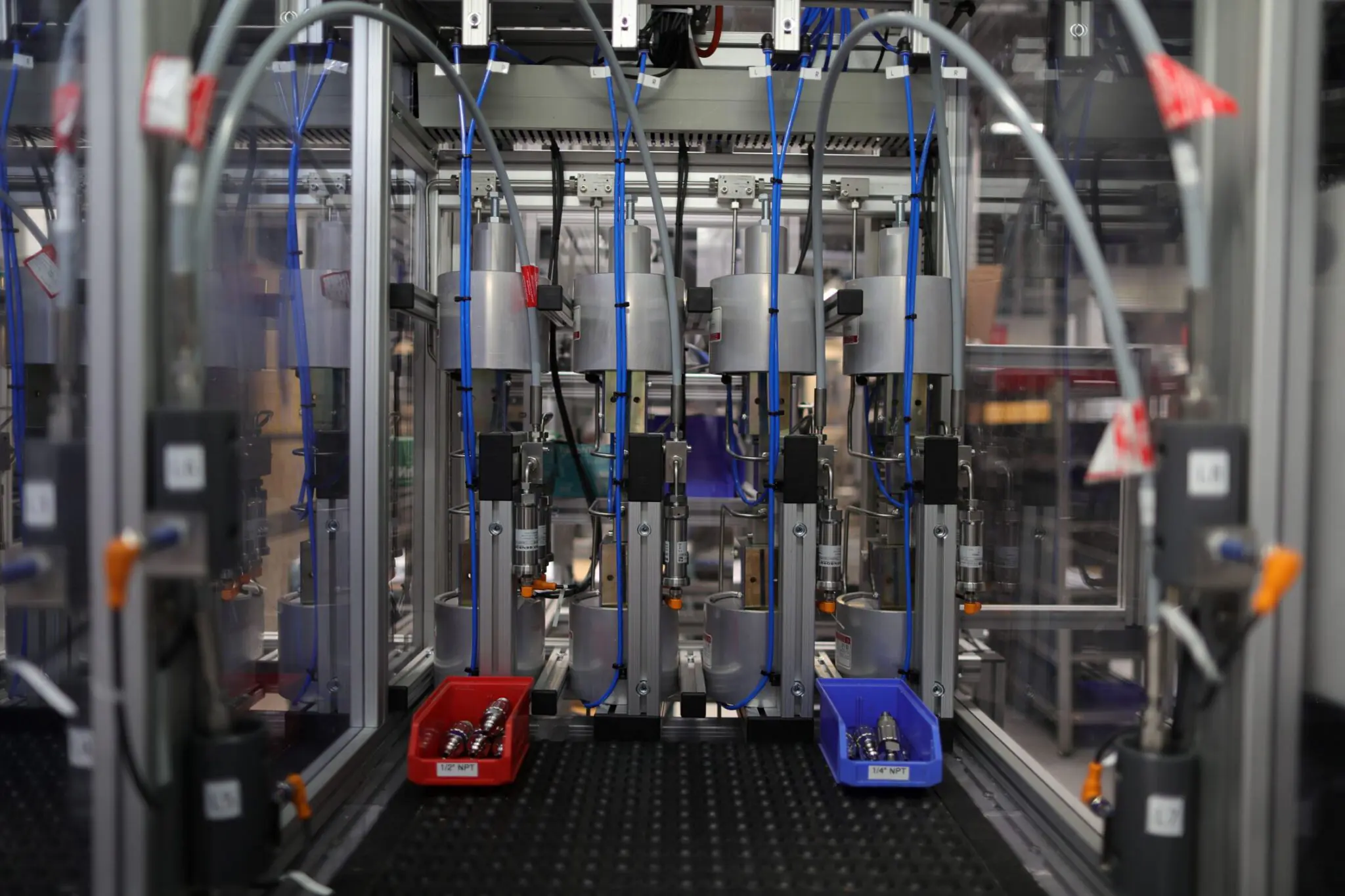