Welding Devices
Optimizing welding quality for complex components
Introduction to the challenge
The goal of producing welds of the highest quality requires a seamless weld to prevent air exclusions and contamination. This requirement represents a major challenge in manufacturing, particularly when manufacturing complex components.
Specialized welding equipment
EPIC & I has developed and implemented special welding devices that are part of the equipment in welding booths. These are essential to meet the high quality standards. Detaching and clamping components and equipping the devices with welding gloves within a few seconds.
Dealing with unconventional component shapes
The main components of the components to be welded are not cuboid but cylindrical and conical, which makes clamping difficult. Special care must also be taken so as not to damage surfaces and paints. The components require welding at several, non-centrally located positions, which makes the use of a turntable complicated and can impair welding quality.
Capillary tubes as additional components
Rolled capillary tubes, which can be up to 25 meters long and have a bundle diameter of around 30 centimeters, represent another element of the challenge. Processing them on a turntable is problematic, as they could interfere with the welding process and twist, which could result in unwanted predetermined breaking points.
Mass derivation as a technical problem
A fundamental problem when welding larger components is mass dissipation, as it is not possible to attach the ground clamp directly. Continuously maintaining the ground connection manually could impair the quality of the welding process, and a clamp poses the risk of damaging the surface finish.
From your vision
to the real solution
Development of innovative welding devices
Conceptual basis
Our solution concept is based on a comprehensive analysis of all possible devices and attachments, followed by an intensive practical testing phase. Based on these findings, we have developed a set of welding devices that can flexibly clamp all types of devices.
Workplace flexibility
This set is available at every welding station, allows employees to work flexibly and minimizes unnecessary walking distances. Ease of use is ensured even with welding gloves, and the precise shape of the devices protects the components from damage such as scratches.
Integration of mass derivation
A particular feature of these devices is their ability to allow mass to be dissipated via the turntable. This makes it unnecessary to install ground clamps and reduces the risk of damage to the components.
Project video
A direct look
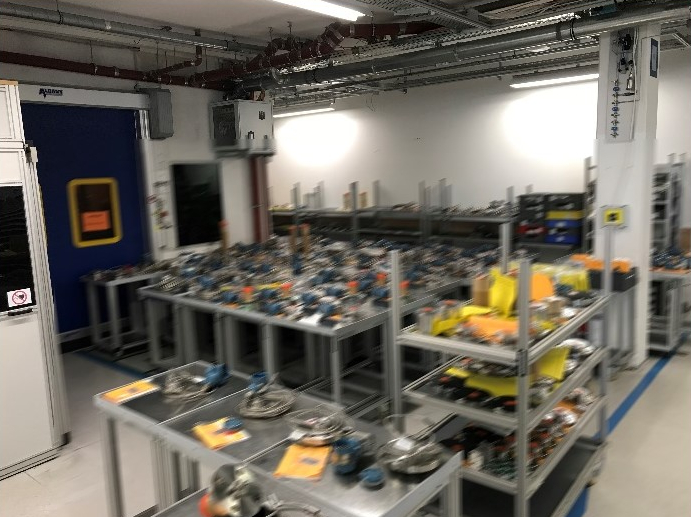
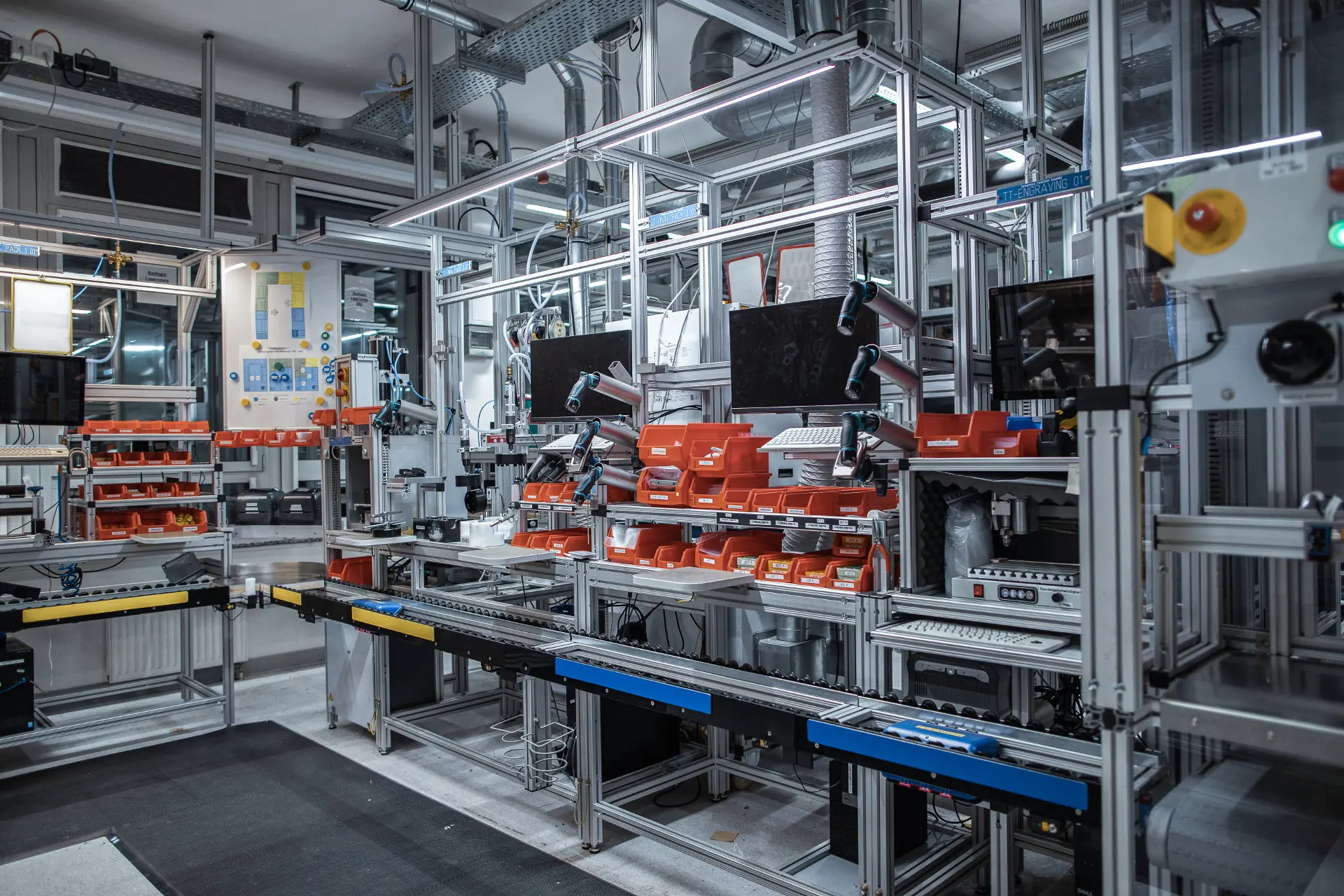